The Comprehensive Guide to Gauge Level Glass: Applications & Advantages
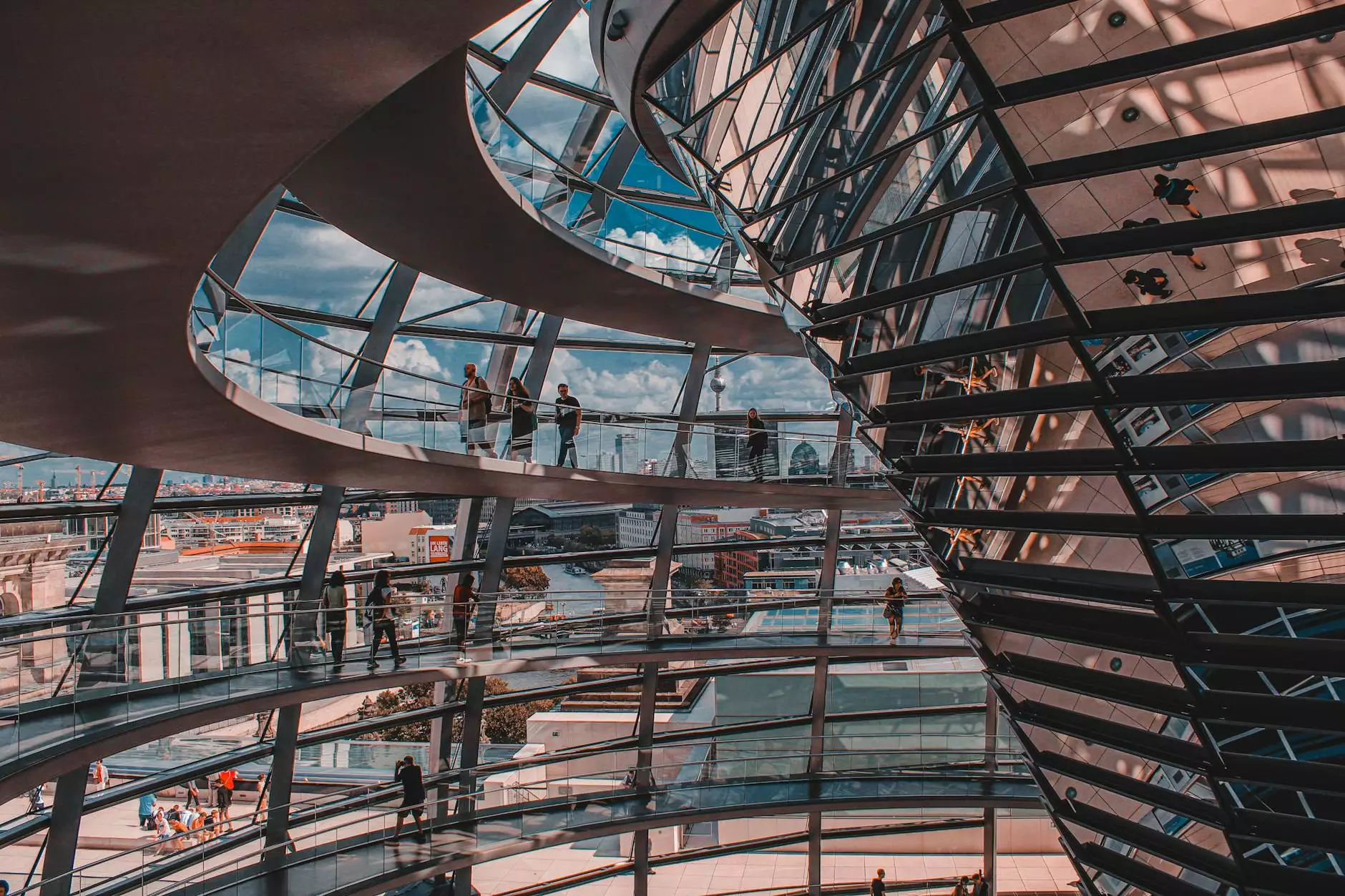
Gauge level glass is an essential component in various industries, specifically designed for level measurement of liquids. Its functionality, durability, and versatility make it a favored choice in sectors ranging from manufacturing to residential applications. In this article, we will explore the applications, benefits, and innovations surrounding gauge level glass, ensuring you have all the information needed to understand its significance and utility.
Understanding Gauge Level Glass
Gauge level glass, also known as a glass level gauge, is a transparent glass tube or panel that provides a visual indication of the liquid level within a container, tank, or boiler. Constructed from durable materials such as borosilicate glass or tempered glass, it withstands high pressure and temperature, making it suitable for a variety of applications.
The Mechanism of Gauge Level Glass
The operation of a gauge level glass is straightforward. It relies on the principle of liquid hydrostatic pressure to indicate the level of the liquid within. When the liquid fills the container, it raises the level within the gauge, enabling operators to visually assess the quantity of liquid present. This simplicity, coupled with efficiency, positions gauge level glass as a pivotal element in numerous installations.
Components of a Gauge Level Glass System
- Glass Tubes: The primary component that provides visibility of the liquid level.
- End Fittings: Essential components that secure the glass tubes to the tank or vessel.
- Isolation Valves: These allow for maintenance without draining the entire tank.
- Float Indicators: In some systems, floats provide additional clarity on liquid levels.
Applications of Gauge Level Glass
Gauge level glass finds applications across diverse industries. Below, we delve into specific sectors and their uses of gauge level glass:
1. Industrial Manufacturing
In industrial settings, gauge level glass is critical for monitoring fluid levels in tanks containing chemicals, oils, and other industrial liquids. Its robust design ensures that it can handle the often extreme conditions prevalent in manufacturing environments.
2. Water Treatment Plants
Water treatment facilities require precise level measurement for the effective treatment and distribution of water. Gauge level glass aids in ensuring that the water levels are maintained, thus facilitating optimal treatment processes.
3. Brewery and Beverage Industry
The brewing process demands accuracy in every phase, from fermentation to bottling. Gauge level glass serves as a vital tool for brewers, providing them with immediate data on liquid levels.
4. HVAC Systems
In heating, ventilation, and air conditioning systems, gauge level glass assists in checking the boiler or coolant fluid levels, which is crucial for system efficiency and safety.
5. Residential Applications
Beyond industrial uses, gauge level glass has found its way into residential applications. Homeowners install gauge level glass in boilers and water heaters, where it serves a critical safety function, enabling them to monitor fluid levels easily.
Benefits of Using Gauge Level Glass
The advantages of gauge level glass cannot be understated. Let's explore some of the key benefits:
1. Visual Clarity
One of the most significant benefits of gauge level glass is its visual clarity. The transparent nature of the glass allows for immediate observation of the liquid level, providing real-time data without needing electronic devices or sensors.
2. Cost-Effectiveness
Gauge level glass offers a cost-effective solution for level measurement. Traditional electronic sensors can be costly to purchase and install, while gauge level glass provides a straightforward and lower-cost alternative.
3. Durability
Built from strong materials, gauge level glass is designed to withstand various environmental conditions. Its durability ensures longevity, reducing the need for frequent replacements.
4. Safety
Monitoring liquid levels is crucial for operational safety. Gauge level glass provides quick visual feedback, allowing operators to respond to potential hazards before they escalate. This aspect is particularly vital in high-risk environments like chemical processing plants.
5. Versatility
Gauge level glass can be adapted for use in a wide range of applications, from industrial furnaces to simple home heating systems. Its versatility makes it an indispensable tool in various settings.
Innovations in Gauge Level Glass
As industries evolve, so do the technologies associated with level measurement. Innovations in gauge level glass have focused on improving functionality, safety, and efficiency. Here are some recent advancements:
1. Advanced Materials
Modern gauge level glasses are made from advanced materials that enhance durability and resistance to thermal stresses and chemical attacks. Innovations in coating technology have further extended the life of gauge level glass.
2. Integration with Digital Systems
Although gauge level glass is traditionally a manual measurement tool, many systems now integrate with digital monitoring systems, allowing for automated level tracking and alerts. This integration combines the best of both worlds, providing visual clarity and advanced functionality.
3. Custom Solutions
Manufacturers of gauge level glass now offer customized solutions tailored to specific application needs. Options such as double-layer glass and specialized fittings allow for a high degree of flexibility in installation.
4. Eco-Friendly Options
In response to growing environmental concerns, some companies are focusing on the development of eco-friendly gauge level glass options. These implementations prioritize sustainable materials and processes.
Installation and Maintenance of Gauge Level Glass
Proper installation and maintenance of gauge level glass are essential for ensuring accurate readings and operational safety. Below are standards and best practices:
1. Installation Guidelines
- Positioning: Ensure that the gauge level glass is installed vertically for accurate readings.
- Securing: Use appropriate end fittings to secure glass panels and prevent leaks.
- Alignment: The gauge should be correctly aligned with the tank to provide an accurate reflection of the liquid level.
2. Maintenance Tips
- Regular Inspections: Check for any cracks or damage to the glass regularly.
- Cleaning: Use non-abrasive cleaners to maintain clarity.
- Leak Testing: Perform regular leak tests to ensure fittings are secure.
Conclusion: The Future of Gauge Level Glass
In conclusion, gauge level glass represents a time-tested solution for liquid level measurement across multiple industries. Its simplicity, durability, and visual clarity continue to make it a top choice for professionals. With ongoing innovations in materials and technology, the future of gauge level glass looks bright, promising greater efficiency and enhanced safety in applications ranging from industrial use to home installations.
Whether you are a business owner looking to implement gauge level glass in your operations or a homeowner needing to monitor your heating systems, understanding the value and functionality of gauge level glass is crucial. Always consult with professionals to choose the right type for your specific needs and ensure installation is carried out to the highest standards.