The Importance of Precision Injection Molds in Modern Manufacturing
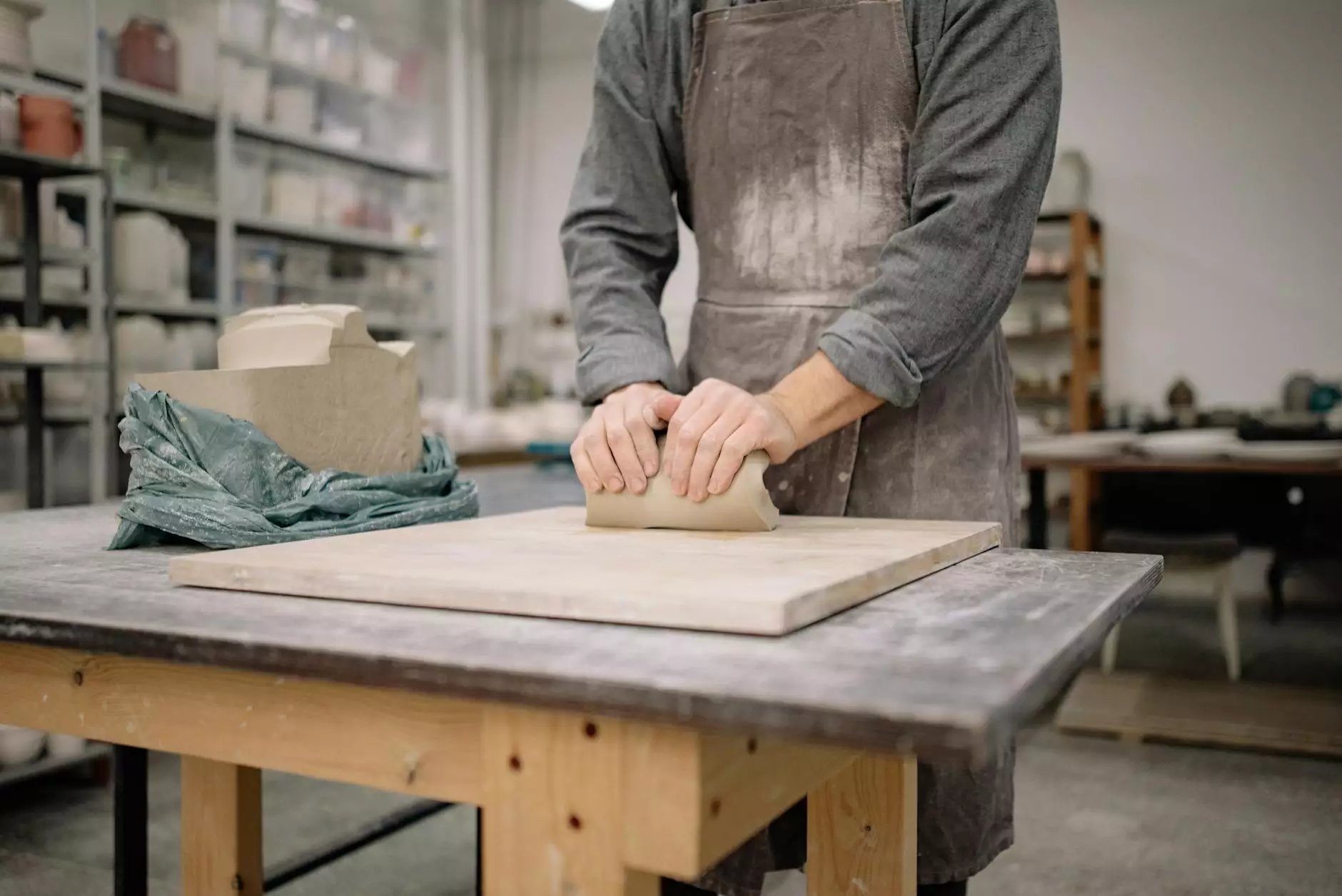
In today’s fast-paced and technology-driven world, precision injection molds have become an essential component in manufacturing processes. The demand for high-quality products emphasizes the need for meticulous engineering and design, with injection molds playing a pivotal role in creating complex shapes and designs efficiently. This article delves into the significance of these molds, their applications, and how they are transforming various industries.
What are Precision Injection Molds?
Precision injection molds are tools used to manufacture parts by injecting molten material into a mold cavity. The materials commonly used include thermoplastics and thermosets. These molds are engineered to produce components with tight tolerances and exceptional surface finishes, ensuring that each part meets the highest quality standards.
Advantages of Using Precision Injection Molds
The use of precision injection molds offers numerous benefits in the manufacturing process, including:
- High Precision: These molds provide unparalleled accuracy, producing parts that fit together seamlessly.
- Increased Efficiency: The injection molding process is remarkably fast, allowing manufacturers to produce large volumes of parts in a short time.
- Cost-effectiveness: While the initial cost of creating a mold can be high, the long-term savings in material use and labor make it a cost-effective option.
- Variety of Materials: A wide range of materials can be used in injection molding, providing flexibility in product design and application.
- Enhanced Surface Finish: Precision molds ensure that the end products have a superior finish, requiring less post-processing.
Applications of Precision Injection Molds
Precision injection molds are utilized across a variety of sectors, showcasing their versatility. Some of the prominent applications include:
- Automotive Industry: From intricate dashboard components to protective covers, injection molding is vital for producing lightweight and durable parts.
- Consumer Electronics: Cases and components for smartphones and other electronic devices are commonly manufactured using precision molds.
- Medical Devices: High-quality, sterile, and precise parts are essential for medical equipment, making injection molding a preferred choice.
- Packaging: Injection molds are used to create efficient packaging solutions that ensure product safety and aesthetics.
- Toys: The toy industry relies heavily on injection molded parts to create safe, colorful, and durable products.
How Precision Injection Molds Enhance Production Efficiency
In a competitive market, efficiency is crucial. Precision injection molds contribute significantly to production efficiency through:
- Rapid Prototyping: Manufacturers can quickly create prototypes to test designs before mass production, reducing time and costs.
- Minimized Waste: The precision nature of injection molding helps maximize material usage and minimize scrap.
- Automation Compatibility: Injection molds can be easily integrated with automated systems, further enhancing production speed and reducing labor costs.
- Scalability: Manufacturers can easily scale production up or down based on demand without major adjustments in processes.
Selecting the Right Precision Injection Molds
Choosing the right precision injection molds is critical for achieving desired manufacturing outcomes. Consider the following factors:
- Material Choice: Select a mold material that withstands the intended use and production volume.
- Design Complexity: Ensure that the mold can accommodate complex shapes without compromising quality.
- Production Volume: Factor in the volume of parts needed to determine mold design and material.
- Supplier Expertise: Collaborate with experienced mold makers who understand your specific requirements.
The Role of Deep Mould in Precision Injection Molding
At Deep Mould, we specialize in providing high-quality precision injection molds tailored to meet the unique needs of our clients. Our dedication to innovation and excellence has made us a trusted partner for businesses across a range of industries. Key features of our services include:
- Custom Mold Design: We work closely with clients to create molds that align with their specific needs and production goals.
- Advanced Technology: Utilizing the latest technology ensures that our molds are not only precise but also durable and efficient.
- Quality Assurance: Every mold undergoes thorough testing to guarantee performance and longevity.
- Comprehensive Support: Our team provides ongoing support and consultation throughout the production process.
Future Trends in Precision Injection Molding
The field of precision injection molds continues to evolve, driven by advancements in technology and changing market needs. Some emerging trends include:
- Smart Manufacturing: The integration of IoT in injection molding operations enhances monitoring and efficiency.
- Sustainable Practices: Increased focus on eco-friendly materials and processes is shaping the future of injection molding.
- 3D Printing Innovations: The use of 3D printing in mold making allows for faster prototyping and reduced lead times.
- Automation and Robotics: Greater automation in production processes is set to increase efficiency and reduce human error.
Conclusion
In conclusion, precision injection molds are a cornerstone of modern manufacturing, offering unmatched precision, efficiency, and versatility. Their applications span across various industries, underscoring their importance in producing high-quality components at scale. With companies like Deep Mould leading the charge in mold design and manufacturing, the future of injection molding looks promising, paving the way for innovations that will shape the products of tomorrow.
Understanding the significance of precision injection molds empowers businesses to make informed decisions that enhance production capabilities and meet the demands of an ever-evolving market. By investing in high-quality molds and partnering with expert manufacturers, companies can ensure they remain competitive and sustainable in their operations.